11 Key Factors to consider when analyzing Manufacturing Costs for New Products

Rolling out new products with 3D printing is not cheap, especially when you are mass producing. Your production budget can be greatly impacted by reducing your manufacturing costs. For your manufacturing costs to be easier on the pocket, you need to consider labor, materials, and overhead costs.
11 Things to remember for Managing Manufacturing Cost
Apply Right Tool for Optimization
It might shock you that many small businesses still manage their time, resources, and staff using old fashioned methods like Excel sheets or paper and pen. Even though these methods are enough for new businesses as they are not good for any company to grow more.
As a result, SaaS software is great for this kind of new company business for payroll, sale points, inventory management, and accounting. If you use the right tools, then you can reduce extra costs due to excessive orders and staff.
Buy Necessary Materials
Many businesses make the mistake of ordering more goods than they need. You cannot access your business' reserve money if you have too much stock. This is why business owners should be careful when ordering supplies. A reliable forecast of future demand based on historical sales trends would be ideal instead of guesswork. If your company is looking for a new revenue stream, you might want to consider a just in time strategy.
Supplier Negotiation
The ability to bargain for a price is a talent that comes naturally to you. It is advised that business owners carefully consider their approach to dealing with suppliers and ensure that they remain strategic when negotiating prices. The first stage in this process is to establish a sincere and reliable supplier relationship. Negotiating money will feel less awkward for you if you establish a good rapport.
Review and Redesign Products and Processes
Products and manufacturing procedures can occasionally become ineffective. It will be ideal to regularly assess your procedures and outputs to determine their worth and potential costs. The items or processes can then be redesigned to be more efficient. For example, a grocery shop owner discovers that his material costs are higher than the standard for the sector. After examining the products, he realizes that one needs more expensive packaging.
The grocery owner calculates the packaging material and compares it to the rest of the products with the same function with no additional cost. But it generally adds more to the total materials costs. He changes the high value packaging material for the normal packaging material used for the rest of the products. As a result, he can save more money than expected because he can bulk purchase the packaging materials. This is why freelance packaging design services come into play for your business.
Costly Material Replacement
Throughout the course of your company's existence, avoid the error of using the exact same raw materials for all of your items. As your business expands, you should also think about using alternative raw materials that result in comparable or identical end goods but are more economically viable. Consider recycling certain resources to create new items or employing less expensive alternatives. Your production expenses might be significantly reduced with the help of these simple adjustments.
Overhead Costs
The overhead costs include gas, electricity, and maintenance of manufacturing sites, uniforms, vehicles, printing, and other related expenses. The reduction of manufacturing overhead may prove to be one of the most effective ways to reduce overall manufacturing costs. Your business can benefit from it by freeing up some cash for other purposes.
Check Your Maintenance Budget
As a necessary evil, maintenance costs are often neglected by business owners. To ensure maintenance costs are not excessive or unnecessary, business owners and managers need to review them regularly.
Check Office and Warehouse Costs
You should also take into account additional costs for your manufacturing enterprises or companies, such as those for uniforms, office supplies, staff vehicles, petrol, cleaning services for staff quarters, security keys, and other unrelated expenses. These little things, like everything else, can mount up, and if you look closely, you can see potential for improvement.
You do not overspend on these smaller costs or pay more than necessary by going through all these smaller costs. If you want to switch brands of office stationery or coffee, you can do so. In the long run, it won't be such a drastic change to your life, but it will save you a lot of money over time.
Rental Expense Review
Many new business owners frequently overlook their renting expenses. It could seem impossible to reduce your spending in this area because it is such a significant outlay. However, regardless of how many sites and warehouses they have, all manufacturing enterprises must routinely assess their rental prices. Take into account the expensive value of the sites' or locations' rent. If not, you might want to consider renting out fewer spaces or fewer rental locations.
Hire Staff as per your requirement
Scheduling employees for shifts without necessity is a common error made by the majority of owners of manufacturing enterprises. Most of the moment, managers will make an educated prediction as to how many employees will be needed for a specific timeframe. Unfortunately, this approach is hit or miss and occasionally leads to over scheduling.
As a result, costs may go up because firms are going to end up paying salaries for employees that weren't really needed to begin with. Your business may want to think about employing scheduling software that can automate the procedure precisely in accordance with the demand in recent weeks to avoid paying these unneeded costs.
Review Staff Wages & Hours
Try to postpone any pay raises until the opportune time when they become appropriate. Additionally, it is critical to communicate with any affected employees in a straightforward and honest manner. If there is anything they can do, like up-skilling, you need to let them know.
To learn more, watch the following video tutorial.
Video Source: California Manufacturing Technology Consulting
One of the costs most closely tied to staff is the staff turnover rate. Due to the ongoing requirement for recruitment, a high worker turnover rate might put your organization at risk of racking up significant expenses.
Additionally, advertising for new hires is necessary and might be costly. It can even be required to work with recruitment companies that can assist with the hiring process. Determine the precise reasons why individuals depart in the first place in order to as much as possible limit staff turnover in order to avoid this issue. You could wish to inquire about the viewpoints of your staff members.
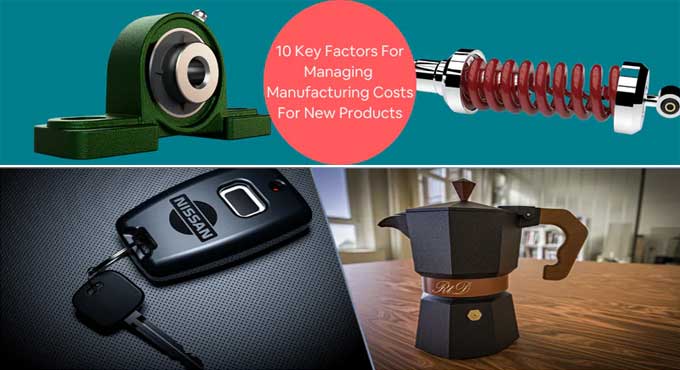